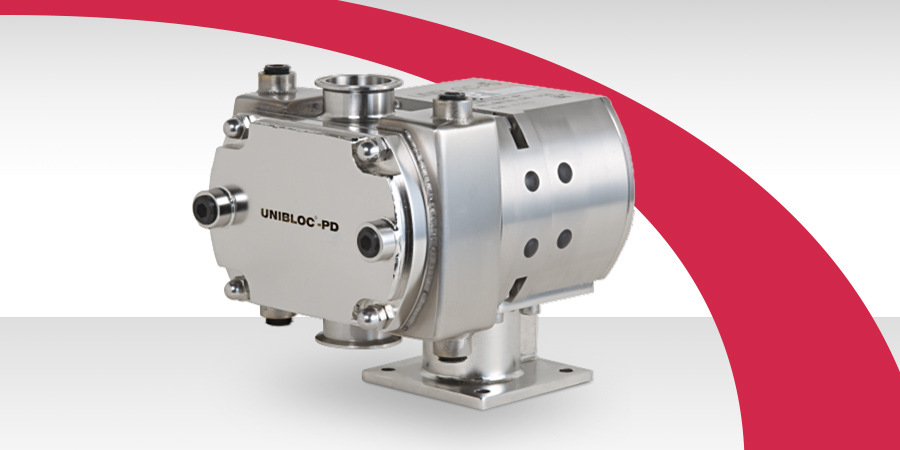
Improved quality control
Gear pumps help enhance product quality controls, leading to significant cost savings to boost the return on investment (ROI) in the pump.
This style pump enhances product quality control by providing precise and consistent flow rates, which ensures accurate dosing and uniform distribution of the transferred substance, maintaining product integrity and minimizing variations. The improved process helps reduce product waste, avoids overfilling or underfilling, and minimizes errors overall in batch production.
Its ability to precisely pump substances with different viscosities supplies this consistency across production runs.
Enhanced quality control reduces the risk of defects. Fewer defects equal fewer customer complaints and costly recalls, ultimately improving operating efficiencies and reducing expenses.
Preventing Contamination
Pump design plays a vital role in preventing potential contamination. A gear pump with a smooth interior, free from gaps or crevices, helps promote hygienic operations. A crevice-free design reduces product contamination. The well-designed gear pump eliminates hidden areas where contaminants accumulate, ensures thorough and efficient cleaning, and leaves fewer opportunities for bacteria product residue or particles to become trapped within the pump.
This reduces the risk of cross-contamination between assorted products or batches, for improved integrity and purity of the substance being pumped.
A design also should simplify and accelerate the cleaning process. It should eliminate areas that are difficult to reach, require extra attention, or specialized cleaning equipment. An efficient or streamlined COP (Clean out of Place) or CIP (Clean in Process) saves time, resources, and equally as important, labor costs.
Unibloc® manufactures its QuickStrip® gear pump specifically designed to facilitate meticulous cleaning. The pumps are engineered to meet stringent standards issued by the Food and Drug Administration (FDA) for its daily cleaning requirements, with Unibloc Pump the leader for 3A sanitary applications.
The QuickStrip design allows tool-free access to pump head and seals. A one-way assembly ensures accuracy and mitigates damage from foreign materials. It minimizes labor and helps reduce the chance of improper pump assembly or lost or damaged parts.
Pump damage incidents during cleaning processes are quite common, accounting for up to 90% of incidences that lead to pump damage or failure. The QuickStrip assembly helps mitigate these risks by reducing the potential for damage.
Its simplified disassembly and reassembly process:
- Minimizes the risk of mishandled components
- Decreases the chance of improper reinstallation of components
- Decreases the risk of lost parts requiring replacement or improper pump functioning
- Lowers replacement and repair costs over time
- Allows for easier access to replace seals, gaskets, or wear rings
- Requires less specialized knowledge and training to operate and maintain
- Allows companies to efficiently allocate labor force
The gear pump style not only saves time and spares labor during the cleaning process, but reduces downtime for production. Its simplified disassembly and reassembly eliminates the need for extensive equipment adjustments, allowing for quicker turnaround times.
It allows operators to maintain high levels of hygiene, minimizes the potential for product contamination, avoids the possibility of pump damage, and supports cost savings by cutting turnaround times for greater operational efficiencies.
Types of industries and applications best suited for a gear pump could include:
- Agriculture: Spraying, fertilizer injection, pesticide application, and irrigation.
- Automotive and transportation: Engine oil circulation, fuel transfer, transmission fluid pumping, hydraulic systems.
- Chemical processing: Acids, solvents, resins, and adhesives, assisting with chemical dosing, blending, and reactor feeding
- Food and beverages: Syrup transfer, chocolate production, dairy processing, sauce and dressing, flavorings. Precise flow control and gentle handling of sensitive products
- Oil and gas: Transfer crude oil, refined petroleum products, lubrication systems, hydraulic systems, and additive injection
- Personal care products: Creams, soaps, cosmetics
- Pharmaceutical and biotechnology: Pharmaceutical ingredient transfer, blending, chromatography, filtration, and processing of biopharmaceuticals.
- Printing and packaging: Ink transfer, adhesive dispensing, coating applications.
Overall, a gear pump from Unibloc® Hygienic Technologies with its QuickStrip® design, provides an invaluable tool for companies seeking optimization of their operations, streamline maintenance and cleaning processes, and reduce costs.
Gear pumps supply efficient and reliable performance by facilitating precise and consistent fluid transfer, minimizing waste, and eliminating cross-contamination to reduce the potential for recalls. By minimizing downtime, reducing maintenance expenses, and streamlining processes, gear pumps can significantly impact a company’s bottom line.
Whether in industrial manufacturing, oil and gas operations, or hygienic applications in the pharmaceutical/biotechnology industries or food processing, any industry that requires fluid transfer can realize substantial cost benefits by incorporating gear pumps into their workflow. This makes a gear pump from Unibloc Hygienic Technologies a smart investment for businesses to maximize profitability.
Call Unibloc Hygienic Technologies today to discover more about our hygienic line of Sanitary 3A gear pumps and our QuickStrip(R) technology.