How Some Meat Processors Are Addressing Labor Issues Using Technology
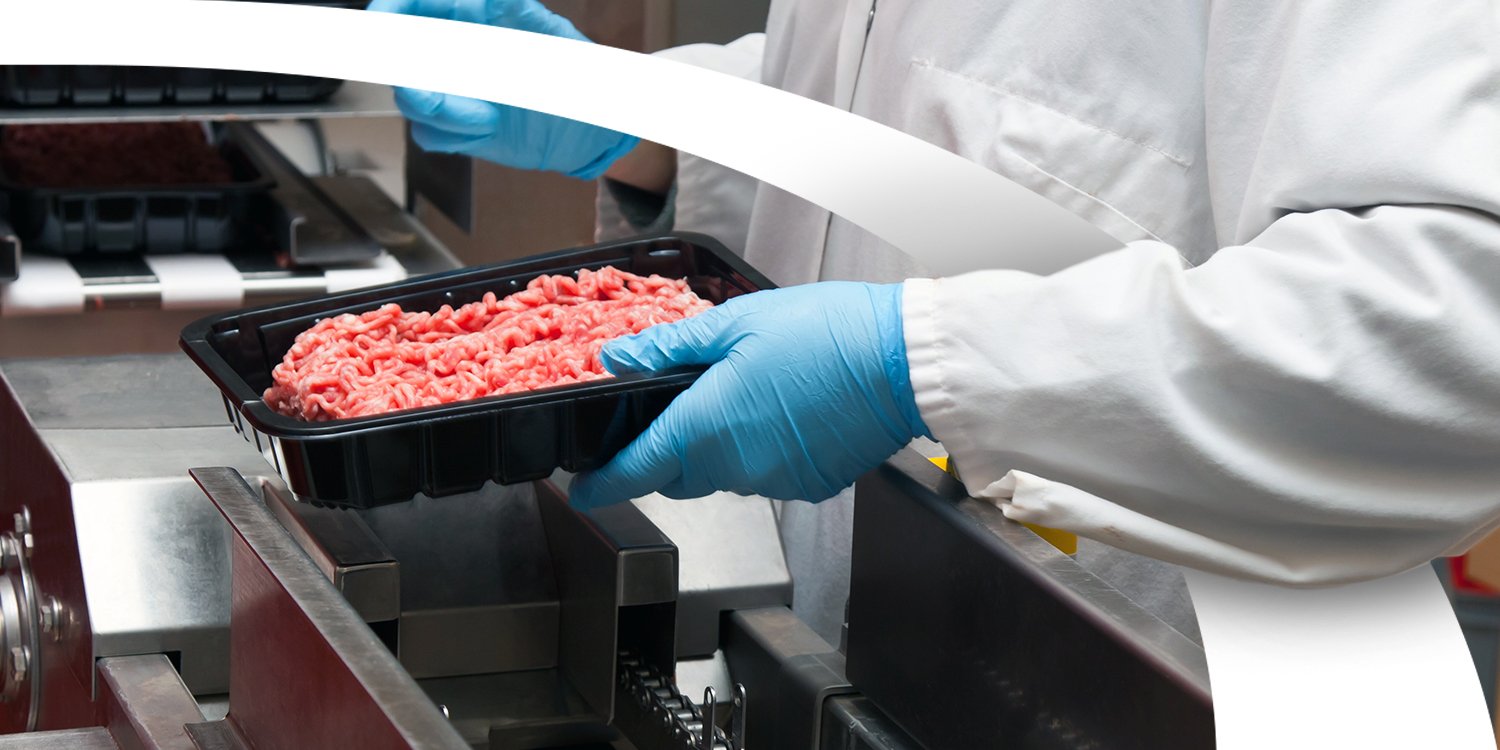
Beef and pork processors have a lot on their plates. Not only must they keep down production costs, they have to do it while managing challenges posed by a scarce and low-skilled workforce. This blog post covers:
- The multiple labor issues for processors and their causes.
- How pump technology addresses labor concerns by helping reduce maintenance times and reducing downtime.
During the COVID-19 pandemic, beef and pork processors were particularly affected, as workers became sick and the workplace did not allow social distancing. At the height of the crisis, plant shutdowns slashed meat processing capacity by about 40%. Labor continues to be a major challenge for the meat processing industry. A recent study from PMMI on Meat, Poultry, Seafood, and Alternative Proteins says that nearly two-thirds of respondents cited labor as their biggest operational challenge. Meat processing facilities require intensive labor and a scarcity of skilled workers negatively impacts operations.
At meat processing plants, labor challenges go beyond a general shortage of skilled workers. After managers find workers, they may experience high staff turnover. Issues around childcare, healthcare, and transportation make it difficult for some people to stay in the workforce consistently. Naturally, beef and pork processing facilities are located close to their suppliers. Rural locations increase the chances that plant workers are driving long distances. When gas prices rise, it’s harder to find and retain workers.
Another issue is that skill levels are uneven, requiring supervisors to provide training and oversight. According to PMMI, 12% of processors say skillsgaps are their top operational concern. The report says that processors are increasing their efforts to train workers and refresh that training. In addition, the supervisor may be newer to the workforce as long-term workers retire.
It doesn’t help these labor challenges that some plant equipment specific to meat processing requires significant labor for maintenance. Pumps that transfer raw ground meat almost always require COP processes on the third shift, which is typically hard to staff in terms of skill level and available workers. Typical pumps have many small parts that need to be removed, cleaned, and properly reassembled, so workers need a certain level of training to complete the tasks consistently and correctly. Training workers on pump cleaning is time intensive. This frequent need for training impacts team efficiency.
Better pump technology can help processors better address labor issues.
Pumps are central to the efficient transfer of ground meat and trimmings. Unfortunately, CIP processes are not able to remove raw meat completely during cleaning, so labor-intensive cleaning is necessary. In addition, like other mechanical equipment, pumps need occasional maintenance by skilled staff, including the time it takes to disassemble and reassemble the pump.
Fortunately, technological advances in pump design can help beef and pork operators better address industry labor challenges. Some modern pumps have design features intended to increase reliability, maintenance and cleaning times, and simplify training.
With a Unibloc QuickStrip® FoodFirst pump, training technicians on how to clean the pump is fast and simple. Because the pump has fewer parts than other pumps, there are fewer steps for workers to learn. Also, technicians can work more quickly because no tools are needed for disassembly and reassembly. What’s more, the parts are designed for one-way assembly, so workers won’t be confused about how to install them.
In addition to making training easier, a modern pump design can reduce maintenance costs by increasing productivity. With a Unibloc QuickStrip® FoodFirst pump, a technician, instead of devoting an hour to cleaning a pump, could spend just 20 minutes, gaining 40 minutes to do other work. Instead of focusing on one thing for an hour, the technician may be able to complete three tasks in an hour.
As the meat industry consolidates processing facilities, time becomes critically important. Cleaning crews have only a few hours to sanitize the entire plant, and this task becomes even more challenging with the addition of more processing lines. Some plants, instead of operating five days a week, extend their operations to six days, leaving less time for technicians to carry out planned maintenance. In large plants operating near maximum capacity, the time savings offered by a fast-to-disassemble and fast-to-reassemble pump quickly add up.
Technological payoff: impact on labor costs and reliability.
There are two things maintenance managers can’t afford: downtime and overspending. Pump design can have a significant effect on labor utilization and operational productivity.
Labor costs:
- Maintenance budgets are getting scrutinized due to rising labor costs. Inefficiencies, like tasks taking twice as long, increase the need for labor. Faster cleaning makes the most of scarce maintenance resources.
- Worker safety impacts labor costs, as well. If a worker rushes through a task and smashes their fingers, their injury can take the worker off the schedule. Of course, the pump’s rotating shaft should be guarded so workers can’t contact moving parts. Pumps designed for safety with simple, tool-free disassembly reduce the chance of worker injury.
Downtime:
- In pork and beef processing, even a single hour of downtime can cost tens of thousands or even hundreds of thousands of dollars. That’s why the maintenance manager’s main goal is preventing breakdowns and ensuring rapid repairs. As the adage goes, time is money.
- Here, again, a thoughtful pump design can help. Unibloc’s patented QuickStrip® technology tackles wear and tear head-on. Rotors and wear pads offer plastic-on-metal contact, eliminating the risk of metal-on-metal damage. In contrast, most circumferential piston pumps are designed with a knob on the front of the rotor that seats into the pump’s front cover. The metal knob is expected to wear over time, which is admitting that the design releases metal into the product.
- A QuickStrip pump uses a universal seal mount, so technicians can choose the optimal seal for the application, reducing the risk of leaks and time-consuming cleanups. Lastly, the cover is supported by a swing arm, so it cannot be damaged or contaminated by dropping it on the floor.
Together, these features translate to increased reliability and significantly lower repair and ownership costs. Watch a video below to see for yourself how our patented QuickStrip technology makes pump maintenance simpler.
Learn more about how Unibloc Hygienic Technologies’ Solutions can streamline meat processing facilities. Visit our beef and pork processing page.