How to Select the Right Barrel Unloader
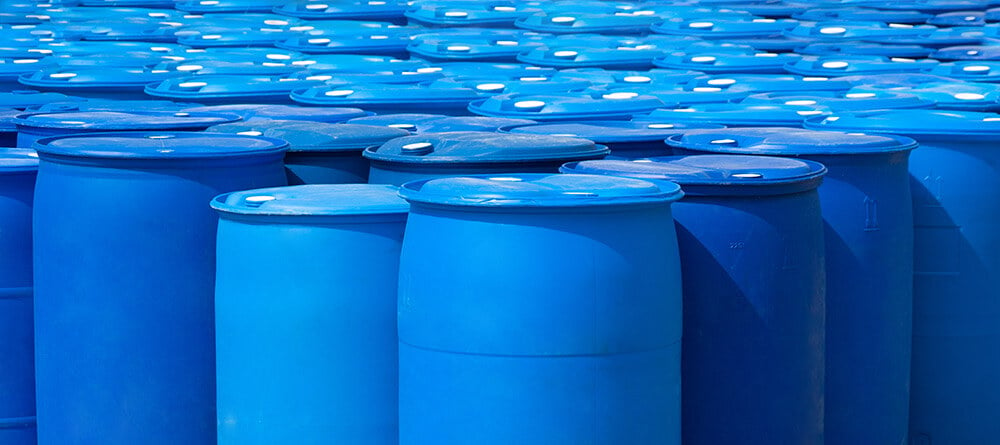
The ultimate guide to choosing a barrel unloading system for process applications.
Whether they contain sauces, cosmetics, or dairy products, barrels are a common sight in food and personal care processing facilities. To ensure sanitary transfer of these materials, hygienic pumps are essential.
Operations managers have different equipment options for this application: a drum unloader (a stick pump) or a barrel unloading system. The barrel unloading systems are further divided into two types depending on the pump: an air-operated double-diaphragm (AODD) pump or a piston pump.
Each type of drum unloader has its advantages and disadvantages. Selecting the wrong barrel unloader pump can mean more maintenance, process interruptions, inadequate flow, or, in the worst cases, no flow at all.
This blog post will help you identify:
- When a barrel unloading system is the right choice,
- which type of system suits your application,
- and what features are available.
Stick pump drum unloaders.
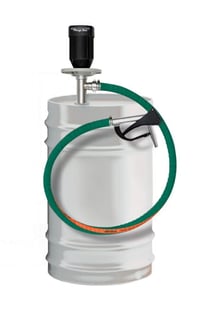
Because the pump is mounted on an intake pipe, people call these drum unloaders “stick pumps.” The pipe enters the closed drum head from above through the drum cap opening. The pipe length is slightly less than the depth of the barrel so it can access the contents at the bottom. In the same fashion, stick pumps can be mounted over IBCs and tote tanks. Often the discharge hose has a manually operated nozzle.
Stick pumps are commonly used for industrial applications where hygiene is not paramount. Also, they don’t apply pressure to the drum contents, so a small amount of material gets left at the bottom of the barrel. For high-value materials, the cost of unrecovered material can add up. The primary benefits of stick pumps include that they are lightweight, easily portable, simple to operate, and very affordable.
AODD-pump barrel unloading systems.
A barrel unloading system is purpose-built for the application and has the advantage of extracting up to 99% of the barrel contents.
A worker places the drum in the unloader. The cover of the barrel must be removed. From above, a wiper plate (also called a follower plate) fits in the opening. The plate has flexible seals that scrape the sides of the barrel as the plate descends. An AODD pump sucks the material and transfers the contents. Pressure from the wiper plate assists the process, enabling fast and efficient unloading.
Piston-style barrel unloading systems.
In contrast, a piston-style barrel unloader does not use suction. Instead of using a pump, the system uses a piston to push down on the plate, creating pressure that transfers the material. Both the piston-style unloader and the AODD-pump-style unloader use compressed air to drive the operation.
Considerations for barrel unloader selection.
Use the considerations below when selecting barrel unloader equipment. If you know what to look for, then you are more likely to achieve an optimal solution for your application.
Mobility. Stick pumps are easily portable, while ongoing processes usually use fixed pumps. Caster-mounted barrel-unloading systems offer the best of both worlds.
Viscosity. Most AODD pumps max out at 100K cP, but when paired with a barrel unloading system, our Flotronic® AODD+ pumps handle up to 500K cP. This is because the unique design of our AODD+ pumps has less internal pipework and, therefore, less friction. Watch this video of a Flotronic Barrel Unloading System pumping silicone elastomer (500K Cp) from a barrel to a mixing vessel… 210 liters in 4 minutes. For extremely high viscosities, select a piston pump. If the specified unloader cannot handle the viscosity of the application, then flow will be restricted.
Self-priming. Access to a barrel is usually from the top, requiring a dry pump to lift material a few meters or more. An AODD pump does not need to be flooded in order to move material. Using a centrifugal pump or lobe pump in a self-priming situation may result in no flow and a process interruption. Piston pumps push rather than suck, so priming is not necessary.
Run dry. If there is an interruption in the flow of material into the pump, such as an empty barrel, the pump could begin to run in a dry condition, which may damage certain types of rotary pumps, and lead to unplanned maintenance. An AODD pump will not be damaged if it runs dry. In any case, a barrel unloading system will automatically stop pumping when the follower plate reaches the bottom of the barrel.
Distance. A piston pump can generate pressure up to 1,200 psi. It is ideal for moving material over long distances because it can overcome the internal friction caused by long transfer lines.
Comparing AODD and piston barrel unloading systems.
- Maintenance workers are already familiar with AODD pumps and their simple design, making maintenance easy.
- AODD pumps are common and often cost less than a piston pump, which is a specialty pump.
- While some AODD-based barrel unloading systems can pump up to 500K cP, they are no match for piston-based systems that can pump up to one million cP.
- AODD pump-based unloading systems work well with a range of viscosities ranging from thin liquids to moderately thick materials. Piston pump unloading systems are usually reserved for high viscosity materials.
If an AODD-based system is the right type for an application, there are still things to consider before a purchase. Not all AODD pumps are designed the same, and some have higher maintenance and operating costs as a result. Here are some advantages of our Flotronic Barrel Unloading System.
- It costs far less than other barrel unloaders that are forced to rely on elaborate piping systems.
- We combined the High Flow Slimline Style AODD+ pump with the Flotronic barrel emptying system. This design enables users to pump highly viscous materials out of a barrel at increased flow rates.
- Depending on the product being transferred, the pump may need to be manually disassembled and cleaned. Our Flotronic Barrel Unloading System incorporates a Flotronic AODD+ pump. Unlike a traditional AODD pump that takes up to two hours to disassemble and clean, the AODD+ pump with the One-Nut® design can be cleaned in only 15 minutes, freeing up techs to do other work.
- It reduces waste significantly by efficiently recovering up to 99% of the barrel’s content thanks to the system’s inflatable seal design. As material costs increase, the ability to completely evacuate the drum becomes more important.
- Over time, fixed seals can relax, allowing leakage around the follower plate. Inflatable wiper seals avoid this problem and enable fine-tuning of the seal for optimum performance.
- Compared to traditional AODD pumps, the AODD+ pump leaves 60% less product in the pump at the end of the production run, saving money on cleaning costs and material waste. This is especially important on high value products in the cosmetics and pharmaceutical industries. For example, an international cosmetics maker was using traditional AODD pump systems to pump finished products from barrels into filling. By upgrading to Flotronic systems, they reduced costly product waste and spent far less time cleaning.
- Because of a design that withstands inlet pressure up to 7 bar, Flotronic AODD+ pumps are the only AODD pumps compatible with Clean-in-Place (CIP) processes. The system can be cleaned in place using the pump itself or an external CIP rig. Other AODD pumps must be removed from the line for cleaning.
For more information about the Flotronic Barrel Unloading System, get a data sheet on our website.