Unibloc's New Sanitary Pump Design Offers Easy Assembly
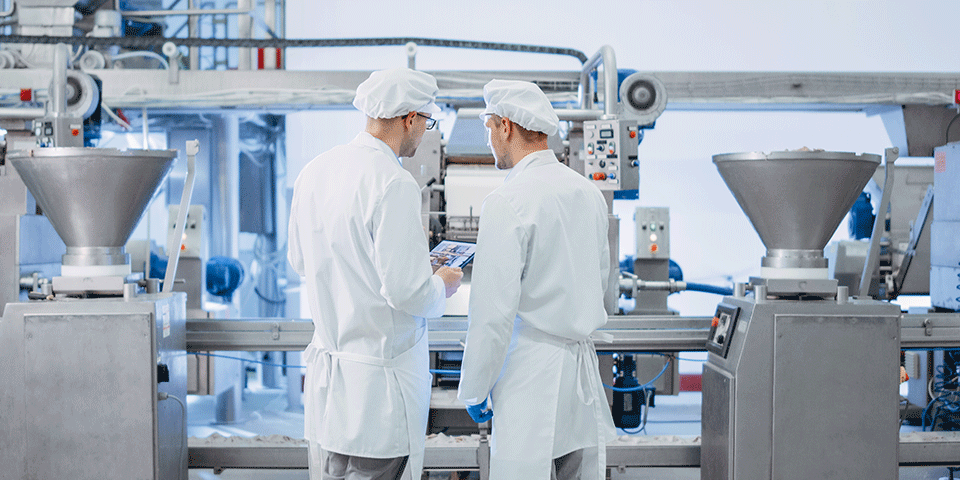
When it comes to choosing the right sanitary pump for your food application, safety comes first. Whether it’s protecting your employees or your customers, sanitation and creating a safe work environment drive every aspect of operational performance for food processors.
Although pumps are standard equipment on every line, there’s nothing standard about the challenges processors must account for when choosing the right sanitary pump for their facilities.
- Daily washdown requires disassembly of the pump, which can cause wear or damage on parts, loss of parts, or incorrect reassembly. Some pumps have as many as 25 different components that need to be removed, cleaned and replaced properly for sanitation. Even small steps taken during daily sanitation can affect your pump – placing covers and parts in a bucket or on the floor can add to the wear on front covers, bolts, rotors and other removable parts.
- Sloppy or incorrect assembly can cause parts and o-rings to become detached from the pump and even enter the food stream. This can be detected to some degree by magnets or metal detectors down the line that can identify foreign objects, if they are metal, but that’s hardly an ideal scenario. In addition, rubber gaskets and plastics that might get accidentally processed in the food are undetectable of course by metal detectors or X-rays.
Actual sanitary pump operation is straight-forward, but not every sanitary pump that claims to be food-grade is equally capable of meeting the food processor’s requirements for safety and sanitation. This is particularly true during the major problems that are introduced during routine cleaning and maintenance operations.
“The sanitation cycle is where 95 percent of the damage occurs to pumps. We’ve always focused there, because making an easier-to-clean pump is an immediate cost savings for any processor,” says Eric Soderstrom of Unibloc Pump.
Every food processor must consider several critical aspects of safety that affect the plant’s sanitary pumps:
- Foreign material contamination risk
- Sanitation process simplification
- Pump reassembly error reduction
- Damage from improper handling
- Transfer mechanics in pumps
Metal-only components
No one wants to face the problems associated with reaching the end of a run only to find that your pump is missing an o-ring, gasket or some other foreign material that could potentially have become ground into the food mix. For that reason, the industry has seen a push towards all-metal parts, so anything that does come loose is picked up in the magnets or X-ray systems that have become standard in every production facility.
High-grade and hard plastic, rubber or other types of components that could experience breakage or disintegration in processing can’t be picked up by X-ray of course. For that reason, today, food and pet food processors are moving rapidly to all-metal solutions.
Designed with the sanitation crew in mind
Daily sanitation is present throughout the processing industry, and the industry has increased its focus on improving practices and procedures for its sanitation crews. The corollary to that, however, is to consider how well the processing equipment you’re considering is designed with daily sanitation in mind. A well-designed piece of equipment must not only consider typical performance parameters such as output efficiency, energy consumption and total cost of ownership, but food processors will also want to know whether it was designed in a way to optimize – and survive – the rigors of daily sanitation and worker safety. When choosing sanitary pumps or any other equipment for your production line, look into critical features such as:- Ergonomic openings, for easy access when cleaning.
- Front Covers with counterweights, easy-swing hinges, or other methods of mitigating the weight of metal openings.
- For large equipment, covers that don’t need to be fully removed for cleaning.
- Protective grills and shields.
- Protective engineering that reduces or eliminates the potential for coming into contact with any sharp or dangerous parts.
Simple, safe, failproof assembly
As mentioned earlier, many safety problems—as well operational costs—revolve around the daily pump sanitation routines. It’s easy and commonplace for complex pumps to be reassembled incorrectly, which can lead to loose or missing parts. The best pumps will be intuitive and quick to reassemble. Fool-proof fitting parts make it easier for the staff and safer for the operation of the machine.
Along with being designed to reduce complexity, it is important to have as few parts as possible. Rotor bolts are one of the most time-consuming to remove and clean, so look for a pump design without rotor bolts which greatly simplifies pump teardown and assembly.
Equipment-friendly maintenance
Incorrect handling during pump cleaning can potentially damage parts and reduce equipment life. It is important to train the sanitation team not to handle the equipment too casually. Simple procedures, such as keeping the pump and its components off the floor, can prevent dents and crevices that can result in poor fitting equipment or lead to contamination and bacteria.
Similarly, tools for disassembly and reassembly need to be used properly. Too much force can unnecessarily damage the pump. Some pump manufacturers today even feature tool-free disassembly and reassembly of their equipment. Tool-free assemblies tend to be easier for the maintenance staff, last longer, and prevent damage and loose parts.
Gentle transfer mechanics
Finally, the inlet to the sanitary pump is one of the areas where material damage can occur. Setting up the production line with gentle transfer mechanics will go a long way to preserving the product integrity and texture. While this isn’t directly relevant to the sanitation requirements, it does ensure product quality and longer pump equipment life over the long term.
Designed for food safety and sanitation
Unibloc's sanitary Pump, for instance, recently introduced its patented, all stainless 600 Series pump design that features no rotor bolts or o-rings, eliminating the most common cause of foreign matter entering food process streams as well as reducing potential for damage during daily washdown (Watch video). Its “QuickStrip FoodFirst” design contains a free-floating rotor design that eliminates bolts and can even be disassembled and re-assembled using no tools to further reduce wear and tear during daily sanitation procedures. The unit also was created with “one-way” reassembly to make it even simpler to maintain.
While it’s unusual to think of a sanitary pump operating without an o-ring, Unibloc Pump engineers designed its new 600 Series to do just that. The units contain no front cover o-ring, which eliminates the tearing or pinching that tend to be common causes of process stream contamination. To simplify sanitation and worker safety, the pumps are the first in the industry to contain a safety swing arm design that allows the front cover to move easily and remain off the floor during washdown.
The fundamental driver for the simplification of pump sanitation is making disassembly and reassembly easy, clean and mistake-proof. Most pumps in the market have bolted rotors and taking apart the rotors is time-consuming and requires the staff to take care with every single part, and carefully reconstruct the machine with proper torque specs.
“We routinely work very closely with the industry’s leading food processors, and several year ago we realized we had to come up with a better approach than the typical stainless steel pump with rotor bolts,” said Soderstrom. “Our customers quickly embraced our QuickStrip FoodFirst design, with its special shims to eliminate all plastic components, fully stainless-steel rotor and far fewer components than a traditional bolt-based system.”
With the safety swing arm on larger models, sanitation crews no longer need to remove and replace multiple bolts to get at the inner mechanisms of the doors. Because these covers seal for a tight fit, the QuickStrip machines don’t require a gasket to ensure the seal in most cases—eliminating another point of failure. Rubber gaskets can tear or incur damage, and fall into the mix—only to be discovered at the end of the day. If the gasket wasn’t recovered in the quality inspection, that’s a day’s work that needs to be recalled. Although this is a rare occurrence in any pump, Unibloc Pump’s gasketless configuration eliminates the problem altogether.
Unibloc's sanitary pump has set up a retrofit program so customers already using earlier models of its QuickStrip series won’t have to replace the entire pump but can upgrade to FoodFirst components.
“The ability to retrofit makes it easier and less expensive for food processors to quickly upgrade to all-stainless pump equipment,”
Learn more about Unibloc Pump’s FoodFirst approach to worker sanitation and food safety.