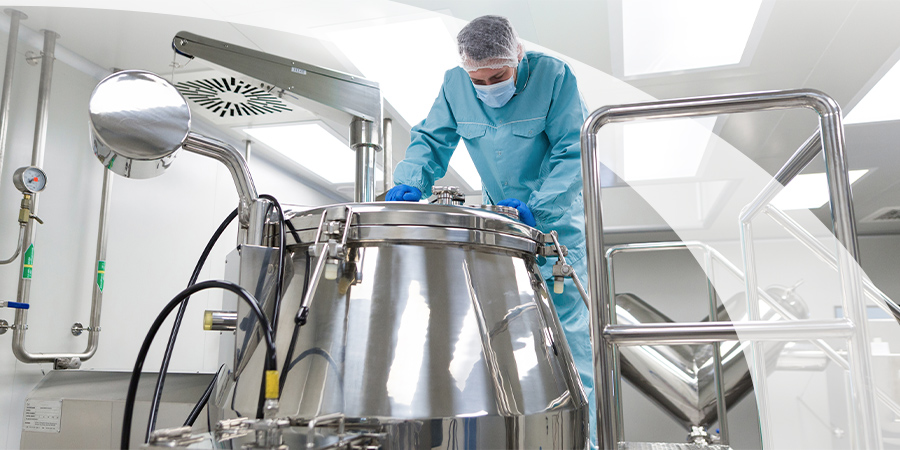
What is a low flow process?
A low flow process refers to a system or operation involving movement or control of fluids at relatively low flow rates. Low flow is dependent on the specific industry, application, or context where a gear pump is running.
In general, low flow operations involve fluid handling or manipulation where precision, accuracy, or control over small quantities of fluid is crucial. These processes often require specialized equipment and techniques to help maintain consistent flow rates, prevent fluid contamination, ensure accurate dosing, or enable precise mixing.
The different industry sectors that rely on low-flow applications include:
- pharmaceuticals
- biotechnology
- chemical applications
- food and beverage
- consumer products (personal care)
- oil and gas
- paints, coatings, and adhesives
Precise metering is essential to a range of applications including ingredient dosing, small batch mixing, laboratory analysis, chemical injection, fluid sample or controlled drug delivery, among others
The low flow is determined by the desired accuracy, precision or specific needs of the application. A low flow rate can range from a few liters per minute down to microliters per minute or even lower to the nanoliter or picolitre per minute range. Ultimately a low flow process is characterized by its emphasis on precise control, accuracy and careful management of fluid movement at comparatively lower flow rates.
Key advantages of gear pumps for low flow applications
There is at least a half dozen key advantages offered by gear pumps in low flow processes
- Precise Flow Control: Gear pumps are known for their ability to provide accurate and consistent flow rates. Offering unrivaled control over the flow of fluids, gear pumps are suitable for applications requiring tight process control.
- Compact size: Depending on the model type, gear pumps are relatively compact. Their small footprint supplies an advantage in low flow processing when space might be limited. The innovative design allows for easy integration of gear pumps into existing systems or installation in tight spaces.
- Self-priming capability: Gear pumps are self-priming, meaning they create a suction to draw fluid into the pump without the need for additional priming mechanisms. If you need to maintain a steady flow of fluid, then self-priming is not a luxury, it is essential.
- High efficiency: Gear pumps achieve high volumetric efficiency, minimizing energy consumption and reducing operating costs. Their efficiency is particularly advantageous in processes where energy efficiency is a priority.
- Low shear: Gear pumps generate minimal shear forces on the pumped fluid, making them suitable for handling shear-sensitive materials or delicate substances. low flow is advantageous when it involves sensitive fluids or products that cannot suffer damage or degradation.
- Wide range of compatible fluids: Gear pumps are compatible with countless fluids, from ultrathin to highly viscous liquids, leveraging their versatility in various low flow applications across different industries. Gear pump features and capabilities
Above all else, the precise flow control is the most significant point in terms of low flow. Gear pumps are:
- Positive displacement pumps, delivering a fixed volume of fluid with each revolution of the gears allowing accurate and repeatable flow rates.
- Output from a metering style pump is directly proportional to the speed of the gears and to the amount of fluid moved via the gear cavity. Precise adjustments in flow are regulated by varying the rotational speed.
- Gear pumps are designed for close tolerances between the teeth and the pump housing. Slippage or leakage between the gears and the pump casing can lead to inaccurate flow rates and other problems. Close tolerances in the gear pump minimize backflow and bypass.
- Capable of reversible flow, operating effectively for bidirectional control of the flow. Changing the gear rotation can allow the operator to adjust or reverse the flow, for greater precision over the fluid movement.
- Offer variable speeds for operators to moderate the flow rate to meet specific process requirements. Fine adjustments allow operators to achieve desired flow rates.
- The speed of the gears and the flow rate are linearly related. Small changes in the rotational speed result in proportionate changes in the flow rate predicting the desired flow rate with a high level of accuracy.
External control options such as flow meters or sensors can be applied to gear pumps or fitted to gear pumps for real time feedback and closed loop control.
Gear pumps offer several significant advantages for low flow processes. Their precise metering capabilities ensure accurate and consistent delivery of small quantities of fluid, making them ideal for applications where precision is crucial. Their compact design allows for easy integration into existing systems, saving valuable space. Their ability to handle a wide range of viscosities makes them versatile and adaptable to various industries and processes.
With their robust construction and minimal maintenance requirements, gear pumps provide reliability and longevity, reducing downtime and operating costs. Moreover, the self-priming nature of gear pumps eliminates the need for additional priming devices, simplifying operation and enhancing efficiency. Overall, gear pumps are a reliable and efficient choice for low flow processes for precise, consistent and cost-effective fluid transfer solutions.
Unibloc Hygienic Technologies (UHT) sets the bar for positive displacement pumps with its engineered design and quality manufacturing. Unibloc operates its own independent manufacturing facilities to provide the highest degree of quality control.
Unibloc gear pumps are designed for the most rigorous processing and cleaning situations. Unibloc Pump is the leader in 3A sanitary applications. The gear pumps feature a seamless, sleek design that eliminates any pinches or gaps where material could build up or conceal hazardous microorganisms. The proprietary QuickStrip® design makes maintenance simpler and easier. It allows for tool-free access to pump head and seals. Simplified one-way assembly and disassembly ensures accuracy, speeds the process, and mitigates damage from foreign materials. QuickStrip is available in both the lobe and gear pump styles. Find the full line of Unibloc’s sanitary gear pumps here or ask about our other types of positive displacement pumps.